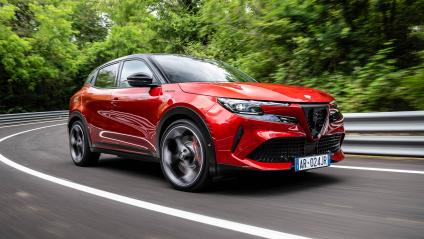
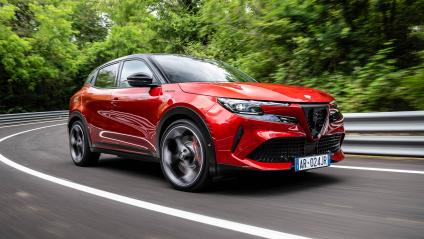
Een lange reis door alle afdelingen in de fabriek.
De eerste races van het seizoen met gloednieuwe F1-auto’s zitten erop. Maar terwijl de teams de hele wereld overvliegen om in alle uithoeken van de wereld te racen, speelt zich op de achtergrond nog een andere race af. De race om de auto’s zo snel mogelijk gedurende het seizoen door te ontwikkelen.
Vooral dit jaar ontwikkelen de teams snel en veel omdat ze overspoeld worden met nieuwe data. Denk bijvoorbeeld aan de vorm van de voorvleugel of de onderdelen ónder de auto die het geheel naar het asfalt moeten zuigen. Waarschijnlijk leren ze elke drie meter wat nieuws.
Maar wat moet er gebeuren voordat nieuwe onderdelen hun weg naar de auto gevonden hebben? TopGear ging op bezoek bij de fabriek van Alfa Romeo Racing om te onderzoeken hoe dit ontwikkelingsproces werkt. In het Zwitserse Hinwil staat de fabriek van het Alfa Romeo F1-team, die Sauber runt. Voordat een nieuw onderdeel vastgedraaid wordt, moet het een reis maken door alle faciliteiten van de Alfa Romeo F1-fabriek, die elk hun eigen rol hebben.
Alles begint bij een idee. Deze ideeën komen natuurlijk niet uit de lucht vallen, maar zijn gebaseerd op cijfers en bevindingen. Door de data van vorige races en resultaten in de windtunnel te interpreteren, zien de ontwerpers en aerodynamica-deskundigen waar er nog wat te verbeteren valt.
De simulator speelt een cruciale rol bij het interpreteren van deze data. Dit gaat iets verder dan een stuurtje van 200 euro en de nieuwste F1-game. De coureur die het ontwikkelingswerk doet zit in een F1-chassis dat op rails gemonteerd is. Die rails kunnen de cockpit naar voren, naar achteren en opzij bewegen en zelfs kantelen. Op die manier worden de bewegingen van de auto in de echte wereld gesimuleerd. Voor de coureur staat een gigantisch scherm.
De simulatiesoftware is voor de mensen achter computers volledig aanpasbaar. Zo kunnen ze, door de data van het circuit in te voeren, ervoor zorgen dat de auto zich in de simulator net zo gedraagt als de echte Alfa Romeo. De tijd die teams krijgen op het circuit is beperkt, maar in de simulator kunnen ze nog veel meer uren en meters maken.
Op die manier kunnen de ontwerpers de auto dus beter begrijpen en zien ze waar de verbeterpunten zitten. Als er een gegrond idee is voor een nieuw onderdeel, wordt dit in meerdere variaties eerst digitaal uitgewerkt en grondig getest.
Deze uitgewerkte digitale schetsen sturen de ontwerpers vervolgens naar de productie-afdeling van de Alfa Romeo F1-fabriek. Die hebben vier grote 3D-printers staan die elk een ander metaal kunnen printen. Deze printers kunnen titanium, roestvrij staal, aluminium en scalmalloy (een aluminium-magnesium-scandium-legering) tot elke denkbare vorm tot een halve meter grootte uithoesten.
Het komt meestal als één onderdeel uit de printer. Dit zorgt ervoor dat onderdelen lichter en steviger zijn. In tegenstelling tot vroeger, waar onderdelen vaak uit meerdere kleine delen bestonden. Toch is het niet zo dat de productie van de nieuwe onderdelen volledig automatisch gaat. Het afwerken van de uitgeprinte onderdelen, zoals het polijsten en verwijderen van overtollig materiaal, moet met de hand gedaan worden en is daarom nog wel arbeidsintensief.
Vervolgens moet de Alfa Romeo F1-fabriek testen of de onderdelen ook daadwerkelijk het gewenste effect hebben. Om dit te controleren gaan de nieuwe onderdelen naar de windtunnel. Hier gaat meer achter schuil dan een ruimte met enkel een grote ventilator. Een metalen buis met een diameter van 6 meter circuleert de lucht rondom een grote ruimte. Voordat de luchtstroom bij de testruimte aankomt, wordt de buis smaller om de lucht samen te persen.
De luchtstroom bereikt hier snelheden van 288 kilometer per uur. Het team heeft een schaalmodel op 60 procent grootte waar de mannen en vrouwen van de aerodynamica de onderdelen kunnen testen door druksensoren op het schaalmodel te plaatsen. Hierbij kijken ze zowel naar de downforce die het onderdeel produceert, als de luchtweerstand die het veroorzaakt. Van de eerste wil je uiteraard zoveel mogelijk, maar de laatste probeer je zoveel mogelijk te verminderen. Als het onderdeel niet doet wat het moet doen, kan het rechtstreeks de prullenbak in.
Vaak is er niet één versie van het ontwerp, maar zijn er meerdere variaties waarbij de hoek steeds één graad scherper is. Daarbij kan het voorkomen dat het omslagpunt van betere naar slechtere prestaties halverwege die variaties ligt. Dat betekent dat een groot deel van die variaties niet eens meer getest hoeft te worden, omdat de resultaten toch slechter zullen zijn. Hierdoor wordt 40 procent van de geproduceerde onderdelen niet eens getest in de windtunnel voordat ze in de prullenbak belanden.
Het liefst ziet Alfa Romeo natuurlijk dat het onderdeel wel gewoon de gewenste prestaties levert. Als dat onderdeel uiteindelijk van koolstofvezel moet worden, kan het team dit ook zelf produceren op een aparte afdeling. Een ontzettend specialistisch werkje waarbij er geen zuurstof bij de onderdelen mag komen bij de productie.
De gecreëerde onderdelen moeten natuurlijk wel tegen een stootje kunnen en kloppend met de regels van de FIA zijn. Het laatste station in de Alfa Romeo F1-fabriek is daarom de kwaliteitscontrole. Het hoofd van deze afdeling vertelt ons dat zij alle nieuwe onderdelen met precisie-apparatuur meten, zodat alles exact aan de reglementen en wensen voldoet. Ook moet dit team ervoor zorgen dat de onderdelen stevig zijn. Is er iets mis? Dan kan het proces, afhankelijk van waar het niet goed ging, weer opnieuw beginnen.
Als het nieuwe onderdeel ook deze laatste vuurproef in de fabriek heeft doorstaan, kan het eindelijk op transport naar het circuit waar de auto zich op dat moment bevindt. In de vrije trainingen kan Alfa Romeo vervolgens kijken of de simulator en de windtunnel goed hun werk hebben gedaan. Het kan namelijk zomaar zijn dat er een verschil zit tussen het gedrag van de auto op het circuit en de bevindingen in de fabriek.
Om te kijken of de updates in de echte wereld werken, kan het team een soort hekwerk met sensoren op de auto plaatsen dat de luchtstroom meet. Ook hebben ze een groen fluorescerende verf tot hun beschikking die tijdens het rijden over de auto verspreid wordt door de luchtstromen rondom de auto. Na een aantal rondjes kan het team aflezen welke route deze flow-vis verf over de auto aflegde om te zien of de luchtstroom in de juiste baan over de auto werd geleid door het nieuwe onderdeel.
Nadat de hele reis van ontwerp, tot productie en testen succesvol is verlopen, zal het nieuwe onderdeel een paar honderdsten winst per rondje geven. Voor zo’n intensief proces waar honderden mensen bij betrokken zijn, lijkt dat misschien weinig. Maar we hebben al vaak gezien dat die paar honderdsten net het verschil kunnen maken in de kwalificatie. En dan is het de investering uiteindelijk toch weer waard.
Reacties